The Complete Guide to Polyaspartic Garage Flooring: Solving Vancouver's Moisture Challenge
Imagine investing thousands of dollars in a beautiful garage transformation only to watch your new floor bubble and peel within months. This nightmare scenario affects many Vancouver homeowners due to our region's unique moisture challenges. At Clever Quarters, we understand that successful polyaspartic garage flooring requires more than just applying a coating—it demands proper moisture management to ensure lasting results. Unlike DIY epoxy kits that often fail within a year, professional polyaspartic systems offer exceptional durability and stain resistance, but only when moisture issues are properly addressed first. This comprehensive guide reveals why moisture management is essential for your garage flooring investment and how professional assessment can save you thousands in potential failures.
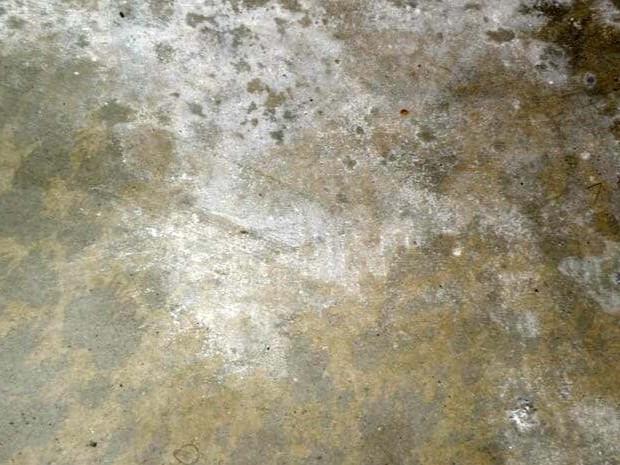
The Complete Guide to Polyaspartic Garage Flooring: Solving Vancouver's Moisture Challenge
Imagine investing thousands of dollars in a beautiful garage transformation only to watch your new floor bubble and peel within months. This nightmare scenario affects many Vancouver homeowners due to our region's unique moisture challenges. At Clever Quarters, we understand that a successful garage flooring project requires more than just applying a coating—it demands proper moisture management to ensure lasting results.
Unlike DIY epoxy kits that often fail within a year, professional polyaspartic garage flooring systems offer exceptional durability, stain resistance, and won't yellow from sunlight exposure. However, there's a critical factor that can destroy even the highest-quality installation: moisture vapor rising through your concrete slab. This comprehensive guide will help you understand why moisture management is essential for your garage transformation success.
Why Garage Floor Coatings Fail: The Hidden Moisture Threat
Think of moisture damage like Vancouver's infamous "Leaky Condo Crisis." Poor building design trapped rainwater, causing rot and structural damage from within. Similarly, polyaspartic coatings create a non-breathable seal on your garage floor. When concrete contains excess moisture, the coating traps vapor underneath, causing bubbling, blistering, and complete coating failure.
The Vancouver Moisture Reality
In our decades of serving Greater Vancouver homeowners, we've documented moisture-related coating failures increasing by 40% in low-lying areas like Richmond and Delta. Rising water tables, climate change effects, and our region's unique geography make professional moisture assessment essential—not optional—for coating success.
Understanding Concrete Moisture in Vancouver's Climate
Your concrete garage floor isn't the solid barrier it appears to be. Think of it as a dense sponge filled with microscopic pores that can wick moisture from the ground below. Even floors that look and feel completely dry can be releasing invisible moisture vapor that will destroy any coating applied over them.
Common Moisture Sources in Greater Vancouver
Groundwater Challenges:
- Annual rainfall exceeding 1,200mm creates persistently high water tables
- Mountain runoff in North and West Vancouver increases seasonal moisture levels
- Poor drainage around foundations allows water to pool against concrete slabs
Construction Factors:
- Many pre-1980 homes lack proper vapor barriers under concrete
- Clogged drain tiles or improper grading direct water toward foundations
- Foundation settlement and minor cracks allow moisture infiltration
Environmental Conditions:
- Coastal humidity maintains higher baseline moisture levels year-round
- Temperature fluctuations cause concrete expansion and contraction
- Freeze-thaw cycles create microscopic cracks that allow moisture penetration
Health and Safety Implications
Moisture-compromised garage floors create more than aesthetic problems. Constant moisture evaporation creates damp, musty conditions that promote mold and mildew growth. Health Canada reports that indoor mold exposure can cause eye and throat irritation, respiratory issues, and worsened asthma symptoms—particularly affecting children and elderly family members.
A properly installed polyaspartic floor system eliminates these health risks while creating a clean, professional space that enhances your home's value and functionality.
The Science Behind Coating Failure
When non-breathable polyaspartic coatings are applied over concrete with excess moisture, failure follows a predictable pattern:
- Vapor Pressure Buildup: Moisture that previously evaporated freely becomes trapped beneath the coating
- Adhesion Loss: Trapped vapor creates pressure that literally pushes the coating away from the concrete surface
- Chemical Attack: Moisture carries alkaline salts from concrete that chemically attack the coating's adhesive bond
- Coating Delamination: Combined physical pressure and chemical attack cause bubbling, blistering, and peeling
Critical Moisture Thresholds
Professional coating systems require concrete moisture levels below specific thresholds:
- Standard polyaspartic coatings: Maximum 75% RH (Relative Humidity)
- High-performance systems: Can tolerate up to 80% RH
- Moisture barrier systems: Required above 80% RH
Professional Moisture Solutions
When testing reveals concrete moisture levels above coating thresholds, your garage transformation project isn't over—it requires professional moisture mitigation.
Moisture Vapor Barrier Systems
Professional moisture barriers use 100% solids epoxy products designed to block vapor transmission and create a dry foundation for polyaspartic topcoats. These systems require precise application and professional expertise.
Professional Installation Process:
Step 1: Surface Preparation
- Diamond grinding removes surface contaminants and creates proper profile
- Mechanical surface preparation ensures optimal barrier adhesion
- Complete dust and debris removal through professional vacuum systems
Step 2: Barrier Application
- Product mixed according to strict manufacturer specifications
- Applied at precise thickness (typically 10-15 mils dry film thickness)
- Consistent coverage essential for effective moisture blocking
Step 3: Curing and Topcoat Application
- Minimum 24-hour cure time before polyaspartic application
- Surface preparation may be required before final coating
- Complete system applied according to manufacturer guidelines
System Limitations
Professional moisture barriers have specific limitations that experienced contractors will clearly explain:
- Cannot stop active water intrusion or hydrostatic pressure
- Will not address foundation cracks or drainage problems
- May not be suitable for areas with severe groundwater issues
- Require proper drainage and foundation maintenance for long-term success
Greater Vancouver's Unique Challenges
Our region's geography and climate create specific challenges that affect garage projects differently across municipalities:
High-Risk Areas
Richmond and Delta:
- Below sea level elevation increases groundwater pressure
- Clay soil conditions restrict natural drainage
- Seasonal flood risk affects foundation moisture levels
North and West Vancouver:
- Mountain runoff creates seasonal moisture fluctuations
- Steep grades can direct water toward structures
- Rocky terrain affects natural drainage patterns
Burnaby and Coquitlam:
- Mixed elevation creates varied moisture conditions
- Urban development affects natural drainage systems
- Older infrastructure may lack modern moisture protection
Climate Factors Affecting All Areas
- Annual Rainfall: 1,200mm creates sustained moisture pressure
- Humidity Levels: Coastal conditions maintain higher baseline moisture
- Temperature Swings: Freeze-thaw cycles stress concrete and coatings
- Storm Events: Intense rainfall can overwhelm drainage systems
Long-Term Value and Investment Protection
A properly installed polyaspartic floor system with appropriate moisture mitigation provides significant long-term value:
- 15-20 Year Lifespan: Professional systems significantly outlast DIY alternatives
- Maintenance Savings: Easy cleaning and stain resistance reduce long-term costs
- Property Value: High-quality garage floors increase home resale value
- Health Benefits: Proper moisture control prevents mold and mildew issues
- Integration Opportunities: Creates foundation for complete garage storage solutions and organization systems
Advanced Technologies and Solutions
Modern moisture mitigation continues to evolve with new technologies:
- Rapid-cure formulations reduce project timelines
- Enhanced adhesion promoters improve bond strength on challenging surfaces
- Hybrid systems combine moisture blocking with decorative properties
- Smart monitoring systems provide ongoing assessment of slab conditions
Protecting Your Investment: Key Success Factors
Getting a perfect polyaspartic garage floor that lasts decades in Vancouver requires following a professional, moisture-focused approach:
Essential Steps for Success
- Never Skip Moisture Testing: It's the only way to predict coating performance accurately
- Use Appropriate Remediation: Vapor barriers prevent costly failures on high-moisture concrete
- Choose Experienced Contractors: Proper installation techniques are critical for system success
- Address Root Causes: Fix drainage and structural issues before coating installation
- Plan for Integration: Consider how flooring fits with overhead storage and organization systems
Warning Signs Requiring Professional Assessment
Contact a professional immediately if you notice:
- White chalky residue (efflorescence) on concrete surfaces
- Musty odors or visible mold in the garage
- Water stains or discoloration on walls or floors
- Previous coating failures or peeling
- Standing water or persistent dampness
The Clever Quarters Advantage
At Clever Quarters, we approach garage flooring as part of a comprehensive transformation strategy. Our moisture assessment process ensures your flooring investment is protected, while our design expertise helps you envision how professional flooring integrates with custom storage solutions to create the ultimate functional garage space.
Our Process
- Comprehensive Assessment: We evaluate moisture conditions, existing concrete condition, and your overall garage goals
- Integrated Design: Our team shows you how professional flooring works with garage cabinets and storage systems
- Professional Installation: Certified technicians ensure proper moisture management and coating application
- Long-term Support: We stand behind our work with comprehensive warranties and ongoing support
Ready to Transform Your Garage?
Don't gamble with your garage flooring investment. Vancouver's unique climate challenges require professional expertise to ensure lasting results. A comprehensive moisture assessment is your first line of defense against coating failure and the foundation for a beautiful, durable garage transformation.
Your garage has the potential to become more than just a place to park your car. With proper moisture management and professional polyaspartic flooring, it can become a clean, organized, and functional extension of your home that you'll be proud to show off.
Ready to start your garage transformation with confidence? Contact Clever Quarters today to schedule your comprehensive moisture assessment and design consultation. Our experienced team will evaluate your specific conditions, explain your options clearly, and provide the expert guidance that ensures your garage flooring will look beautiful and perform flawlessly for decades to come.
Let us give you the peace of mind that comes with professional diagnosis and the perfect foundation for a garage that truly enhances your home and lifestyle.
Frequently Asked Questions
Can your polyaspartic garage flooring be applied over a suspended slab?
Yes, our polyaspartic garage flooring can be applied over a suspended slab. However, it's important to note that while polyaspartic coatings have excellent elongation properties, they are not inherently waterproof. If your garage floor doesn't have built-in waterproofing system installed, we recommend the application of a waterproofing membrane prior to the polyaspartic flooring. Specifically, we use Sikalastic 390 as a waterproofing membrane. This is applied after the concrete grinding and surface repair, ensuring the floor is both durable and protected from potential moisture issues before the polyaspartic coating is applied.
I'm considering doing my garage floor on my own. Why should I choose your company instead?
Here's why many homeowners trust Clever Quarters for their garage flooring:
- Expertise: Our seasoned team ensures a perfect, long-lasting finish.
- Premium Materials: We utilize top-tier products not typically available for DIY projects.
- Efficiency: We're trained to get the job done swiftly, reducing any inconvenience.
- Surface Preparation: Our equipment prepares the floor for optimal coating adhesion.
- Assured Warranty: We stand by our work, offering a 15 years warranty for peace of mind.
- Durability: With our professional touch, your floor will not only look fantastic but will also stand the test of time.
Can you install polyaspartic flooring over a garage floor with an in-floor heating system?
Yes, polyaspartic flooring can be installed over a garage floor with an in-floor heating system. Polyaspartic coatings are known for their ability to withstand temperature fluctuations, making them compatible with heated floors.
Why do you test the concrete hardness and how do you treat soft concrete differently than hard concrete?
Treating soft garage concrete floors requires a specialized approach compared to regular concrete, especially when it comes to floor preparation.
Before any work begins, it's crucial to assess the softness of the concrete using a concrete hardness tester. Soft concrete often has a powdery surface and can be easily scratched.
In situations where we are dealing with soft concrete floor, we need to apply a special primer layer specifically designed for soft or porous concrete to enhance the bond between the concrete and the subsequent coating.
Soft concrete can sometimes retain more moisture than harder concrete. It's essential to check the moisture levels before applying any coatings. If moisture levels are too high, specific moisture barrier products might be needed.
What's the difference between epoxy and polyaspartic garage flooring?
When comparing epoxy and polyaspartic garage flooring, several key differences emerge. Epoxy flooring, takes longer to cure. It's also more sensitive to temperature variations, which means it might not set properly under extreme conditions. Additionally epoxy can yellow over time, especially when exposed to direct sunlight like in garages.
On the other hand, polyaspartic flooring offers rapid curing, often setting within just a few hours. It boasts the ability to be applied in a wider range of temperatures and has superior hot tire resistance. Polyaspartic is UV stable, meaning it won't yellow in sunlight, and it's more resistant to chemicals and abrasions than epoxy.
About The Author
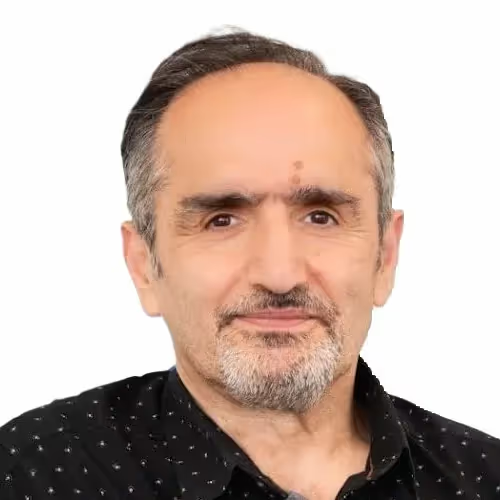
Askari, founder of Clever Quarters, specializes in transforming homes through smart organization and design. His passion lies in leading a talented team committed to creating functional, aesthetically pleasing spaces. Under his guidance, Clever Quarters has become synonymous with enhancing everyday living through thoughtful organization
Ready to Transform Your Space?
An organized home is closer than you think. It all starts with a friendly conversation about the possibilities for your space. Contact us today to schedule your complimentary, no-obligation design consultation with one of our expert designers.
Related Posts
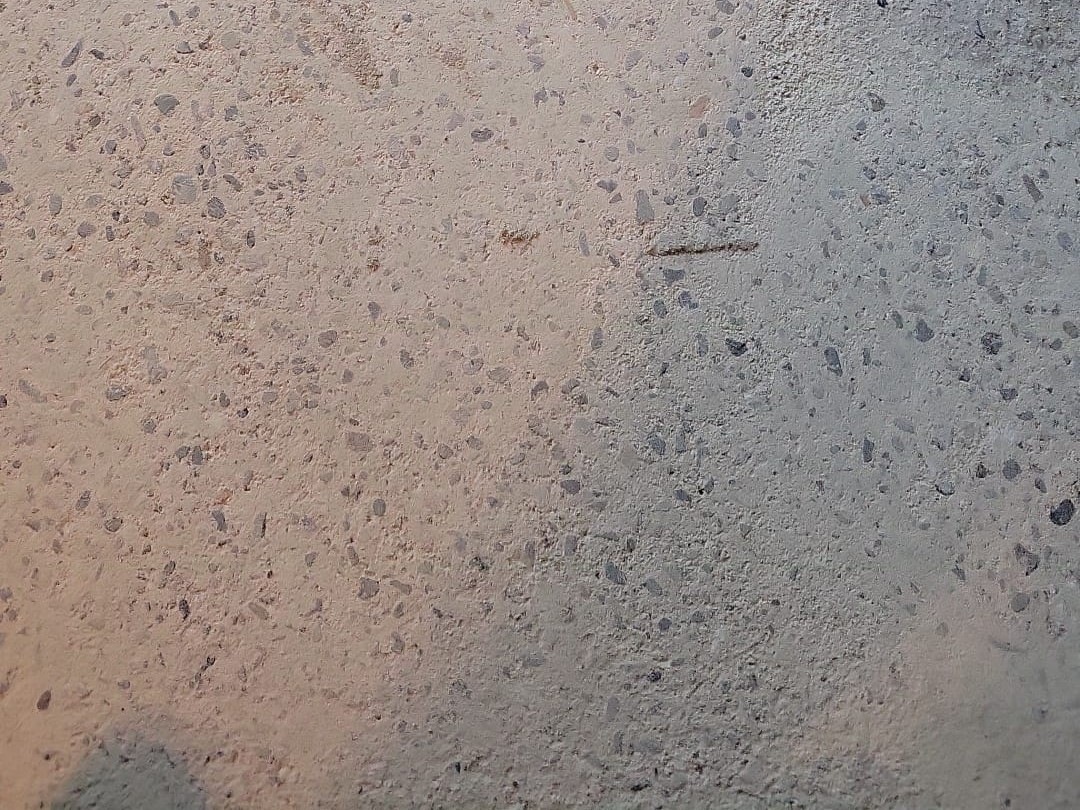
The Unyielding Truth About Soft Concrete and Polyaspartic Floors: Why Primer is Non-Negotiable
Transform your garage with a stunning polyaspartic floor, but beware of soft concrete! Discover why proper priming is non-negotiable for a durable, long-lasting finish and how Clever Quarters ensures your investment endures.
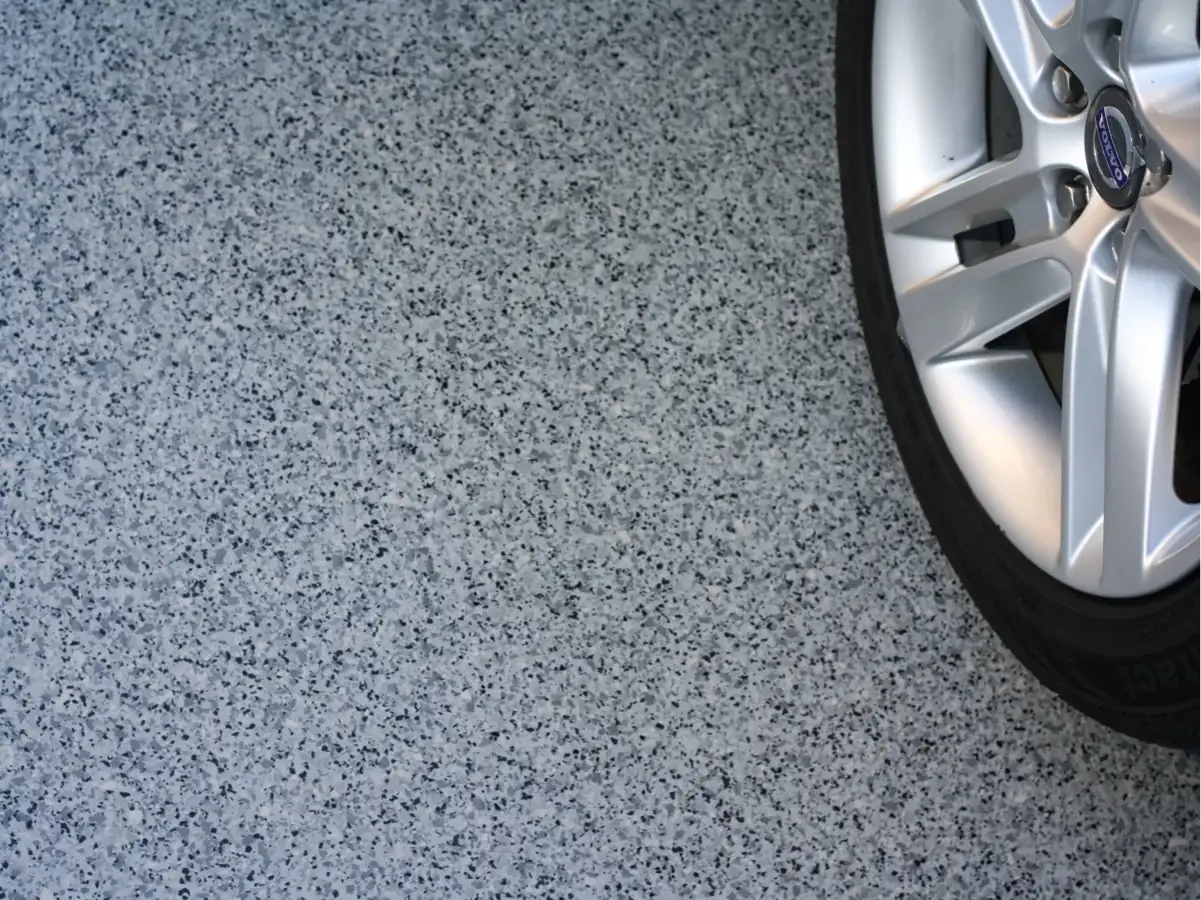
Garage Floor Coating for Suspended Slabs in Vancouver: Why Waterproofing Matters
Suspended garage slabs can leak and damage rooms below. Learn why a Sikalastic 390 waterproofing membrane, followed by a polyaspartic coating, is the gold-standard system for Vancouver homes—and how Clever Quarters installs it right the first time.
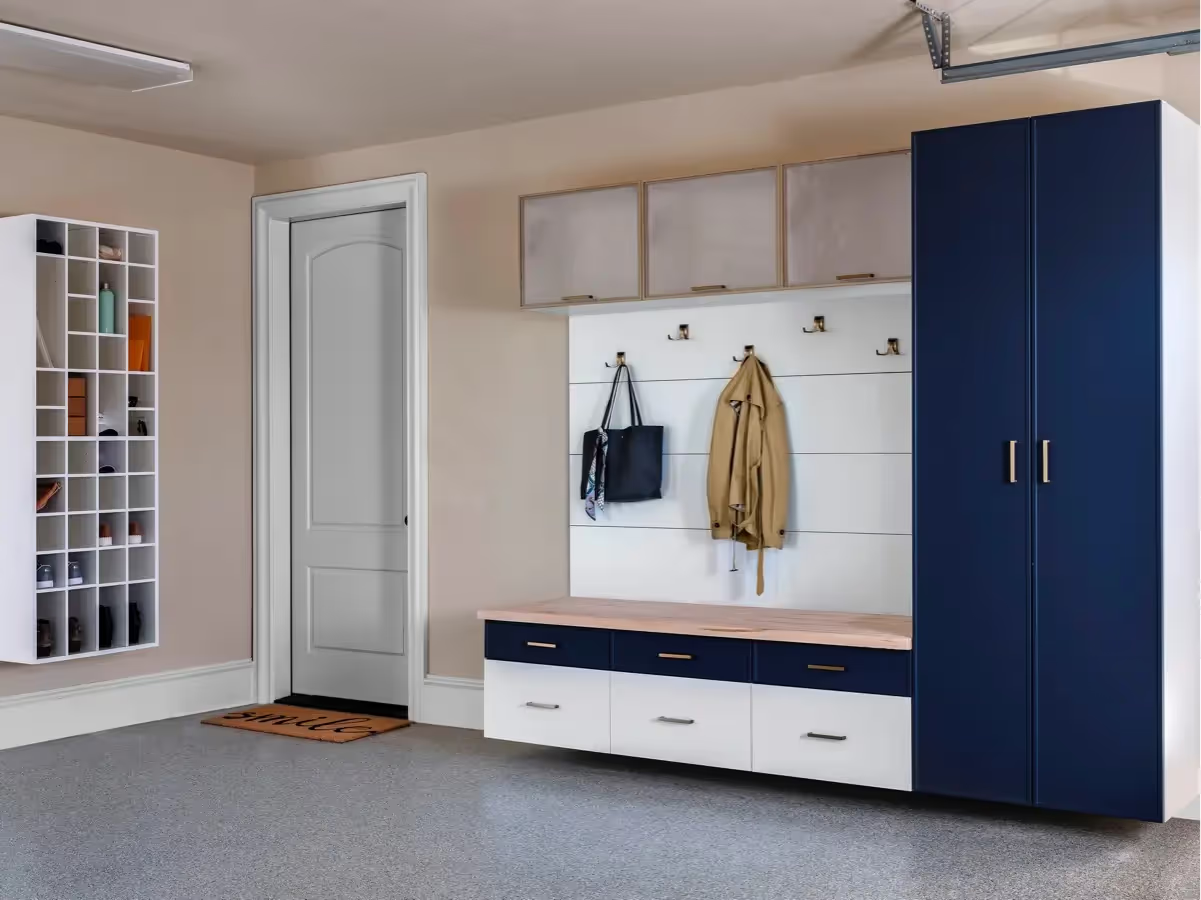
From Garage to Haven: Elevate Your Home with a Functional Mudroom by Clever Quarters
Discover how Clever Quarters can transform your garage into a functional, stylish mudroom. Learn about custom storage solutions, durable construction, and our client-centric design approach to enhance your home's efficiency and harmony.